Damage detection in the composite wind turbine blade for bridge applications
Many composite wind turbine blades are now reaching the end of their design life, prompting exploration of innovative ways to repurpose them. In collaboration with Rzeszów University of Technology, a blade segment was tested using multiple surface-mounted optical DFOS fibers. This approach transformed the structural component into a large 3DSensor, capable of self-diagnostics by measuring strain (με) and calculating displacements (mm).
DFOS Sensors Installed: Optical fibre in acrylate coating
Project challenges
Benefits of using the DFOS monitoring system
Results of using the DFOS monitoring system
Six measurements lines were installed on the surface of a composite wind turbine blade at different positions around the cross-section. After dynamic reading during load cycles, the component was loaded statically. The DFOS-based system allowed not only for strain and displacement measurements over the entire length but also for the identification of safety-critical cross-sections and the fracture itself.
Technical specifications
Example results
Recomendations (optional)
Lorem ipsum dolor sit amet, consectetur adipiscing elit, sed do eiusmod tempor incididunt ut labore et dolore magna aliqua. Ut enim ad minim veniam, quis nostrud exercitation ullamco laboris nisi ut aliquip ex ea commodo consequat.
John Doe
Project partner
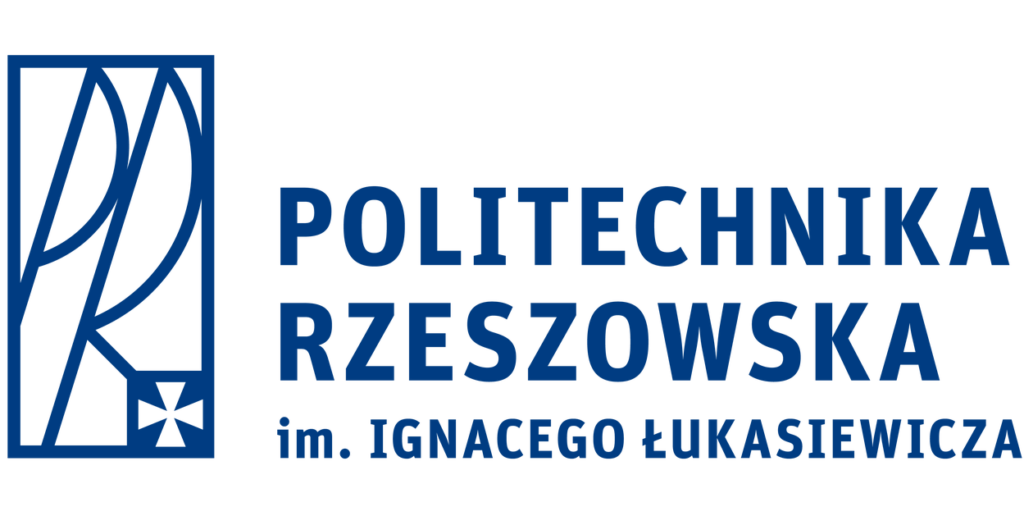